'Stages of Clay'
- Neha Gopinath Pillai
- Feb 7, 2019
- 2 min read
Hello!
This post is all about the stages of natural clay explained with images in a simple manner to both artists as well as end users/customers. To artists, especially beginners this will be useful from a working point of view and for the customer it will help with product awareness. (know what you buy!)
The six stages are:
Slip
Plastic or wet clay
Leather Hard clay
Bone dry
Bisque ware or fired pieces
Glazeware
Slip - A mixture of water and clay which acts as a glue that helps hold /attach two individual pieces of wet clay. Its a thick, creamy texture of clay. Refined or strained slip can be used in slip casting or trailing.
Plastic or The wet clay stage - clay literally right out of your plastic bag! Its at this stage you prepare your clay. Can be easily molded at this stage. For me, this is where I knead and roll the clay into a slab before proceeding further. I conceptualize the design and start working towards it.
Leather hard - The clay is firm yet moist at this stage. A state of clay where one can do designs, cravings, cut works etc. The flexibility of clay at this stage is poor, hence if the slab of clay is bent it will break. For those into terracotta jewelry designing, inserting the nichrome pins at this stage is ideal, but wait any longer and there is a high possibility that portion will crack.
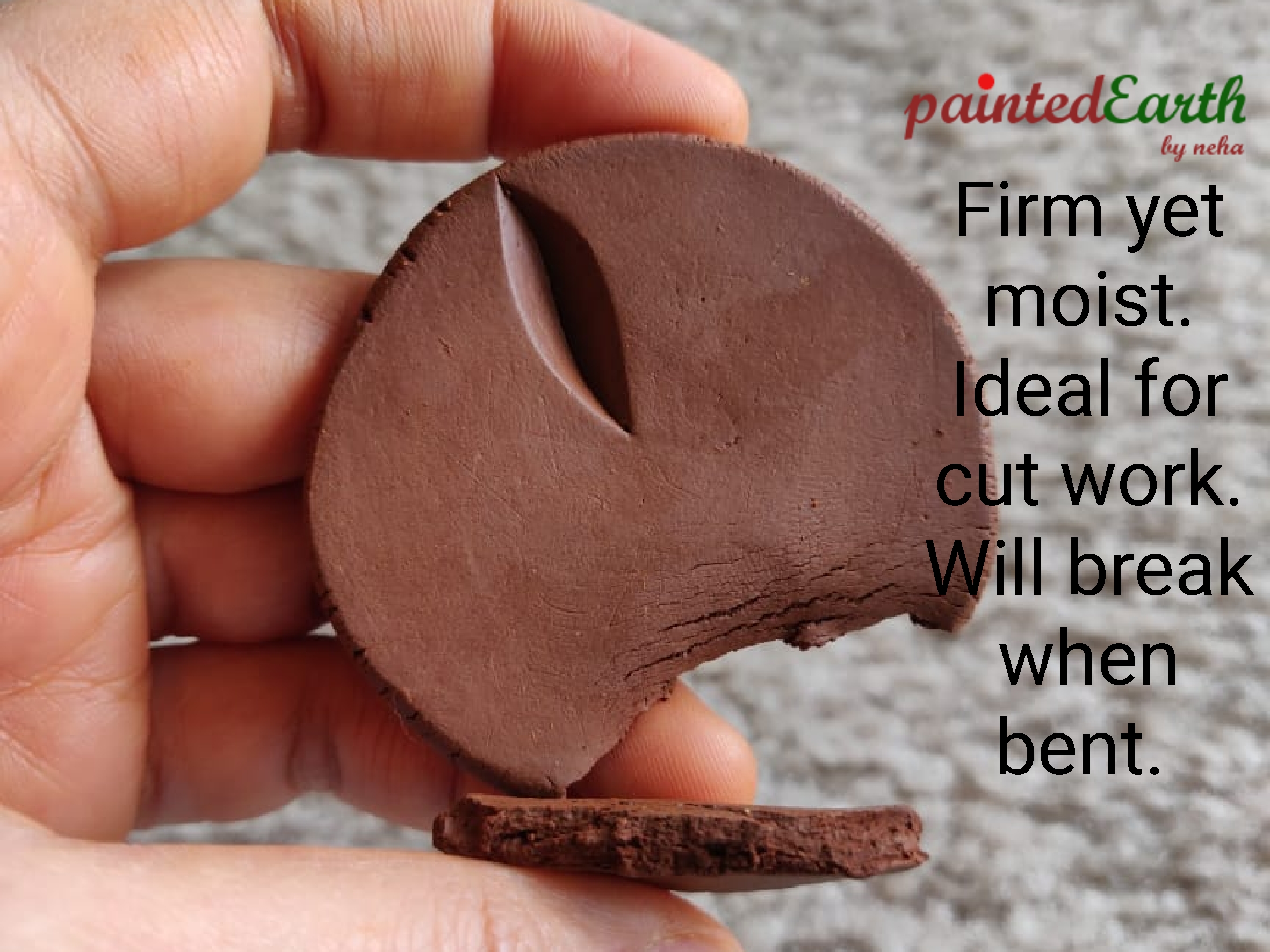
Bone dry - The state where the moisture content in clay has been drastically reduced. One can clearly see the difference in color at this stage. The clay is no longer cool to touch. This stage is usually achieved in a couple of days based on the external factors such as weather. One must make sure the pieces are dried well, as any amount of moistness in the clay can cause damages to the pieces when fired in the kiln.

Clay is called 'green ware' in all the above mentioned stages.
Bisque ware - The fired pottery is called bisque ware. At this stage the pieces are more rigid and the moisture content is completely sapped out of the clay. Low fire earthenware clay contains iron and other minerals which cause it to reach optimum hardness between 900℃ and 1100℃. The clay has matured but it is still porous. One can paint or glaze over it. Glazing would require it to go back into firing which would be the last stage of clay.

Glaze ware - Glazes are applied and fired making the pottery non-porous, creating a glass like covering, hence waterproof and functional. I don't glaze so I have limited information on the topic therefore no images to share.
I sincerely hope you find this information useful. It has taken me some time and effort to draft this in the easiest way possible. I request the readers to not misuse this article or its content. If you would like share, please do it from the source (share the link) so its traced back to me. This is an ethical practice.
Thank you to all those who took some time out to give this article a read.
YouTube link: https://youtu.be/ZLDhJAJfkVw
Neha Gopinath Pillai
Comments